Methods for making resin models using liquid mold silicone
Prepare a polished resin master mold to ensure the gloss of the master mold.
Knead the clay into a shape that matches the resin model, and drill positioning holes around the perimeter.
Use a template to make a mold frame around the clay, and use a hot melt glue gun to completely seal the gaps around it.
Spray the surface with release agent.
Prepare silica gel, mix silica gel and hardener in a ratio of 100:2, and be sure to mix thoroughly.
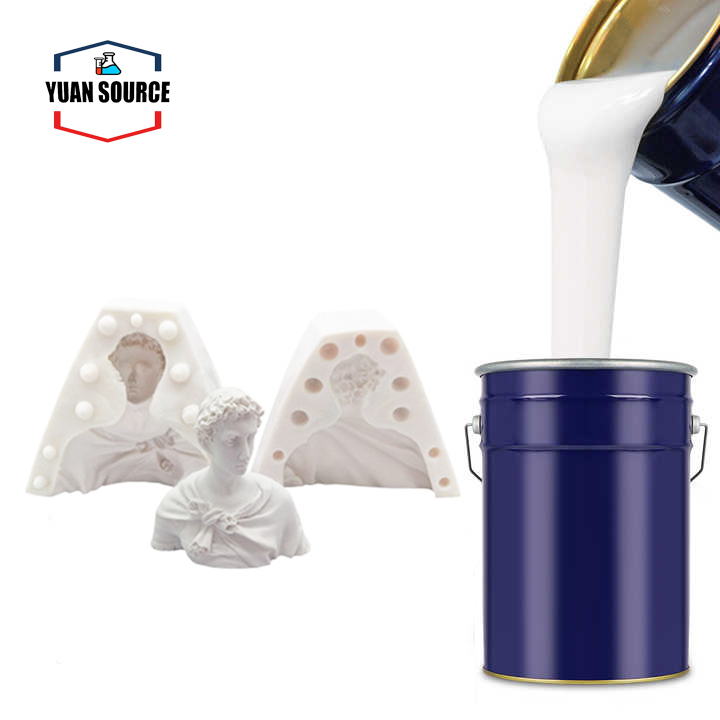
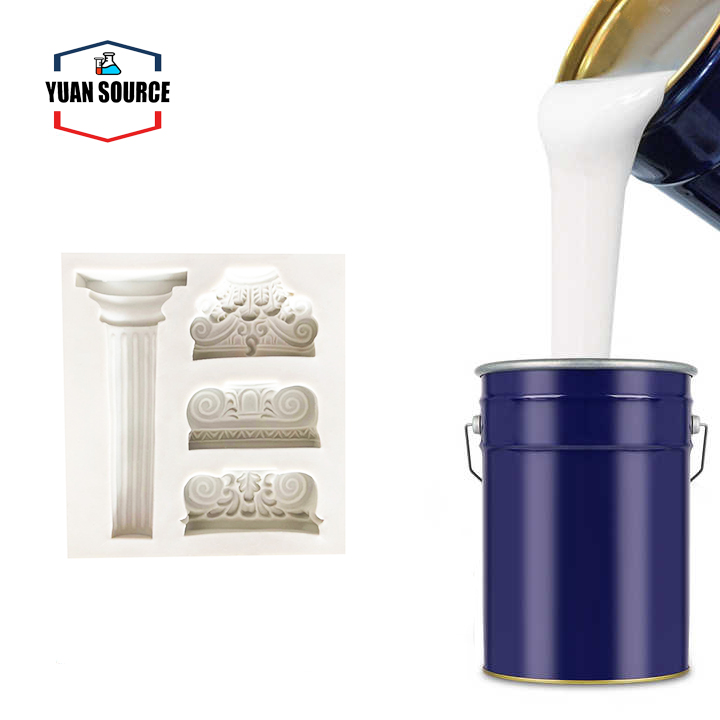
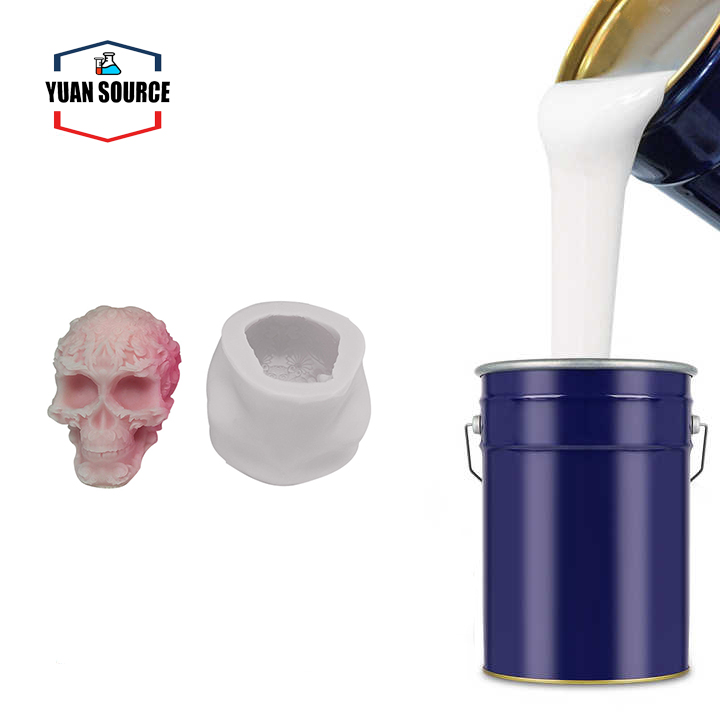
Vacuum deaeration treatment.
Pour the mixed silica gel into the silica gel. Slowly pour the silica gel into filaments to help reduce air bubbles.
Wait for the liquid silicone to completely solidify before opening the mold.
Remove the clay from the bottom as shown below, turn the mold over and repeat the above steps to make the other half of the silicone mold.
After curing, remove the mold frame to complete the production of the two halves of the silicone mold.
The next step is to start replicating the resin. Inject the prepared resin into the silicone mold. If possible, it is best to put it into a vacuum to degas and remove bubbles.
After ten minutes the resin has solidified and the mold can be opened.
Application characteristics of resin sculpture mold glue
① It has excellent burning resistance, and the high temperature resistance can generally reach 100℃-250℃, which can effectively solve the problem of the resin product releasing heat during the curing process and causing the silicone mold to be burned out.
② No oil leakage, increase production efficiency and improve product surface integrity.
③The hardness, viscosity, and operating time of silica gel can be produced according to customer needs, and silica gel can be customized for you.
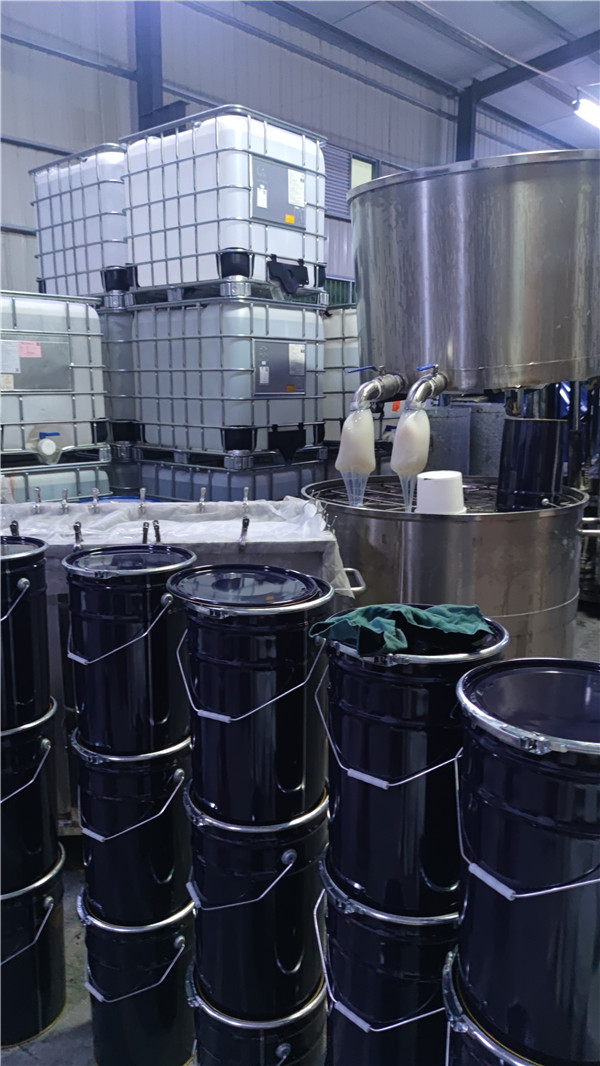
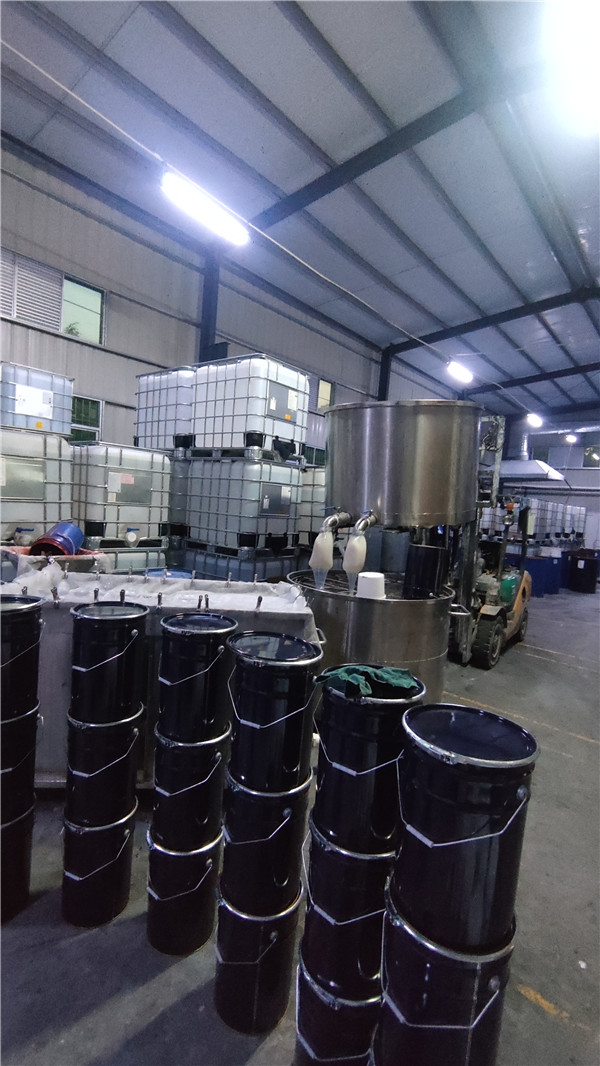
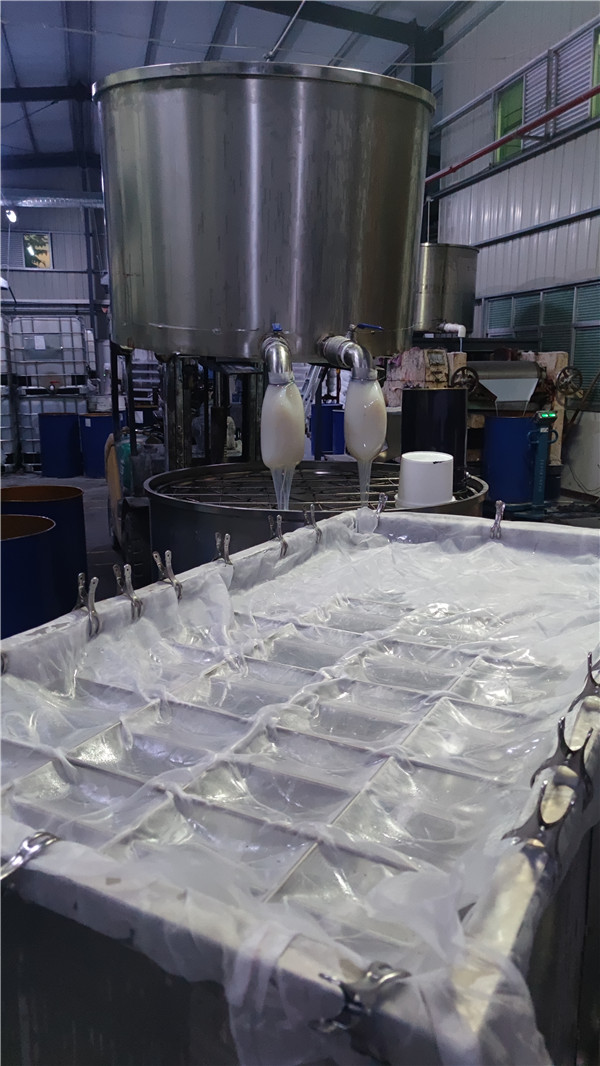