Different silicone hardnesses have different application ranges
0 Shore A and 0 Shore 30C hardness. This kind of silicone is very soft and has good Q-elasticity. It is often used to make finished products that simulate certain parts of the human body, such as chest pads, shoulder pads, insoles, etc.
5~10 hardness. It is suitable for filling and flipping product models with very fine patterns and easy demoulding, such as the production of silicone molds for soaps and candles.
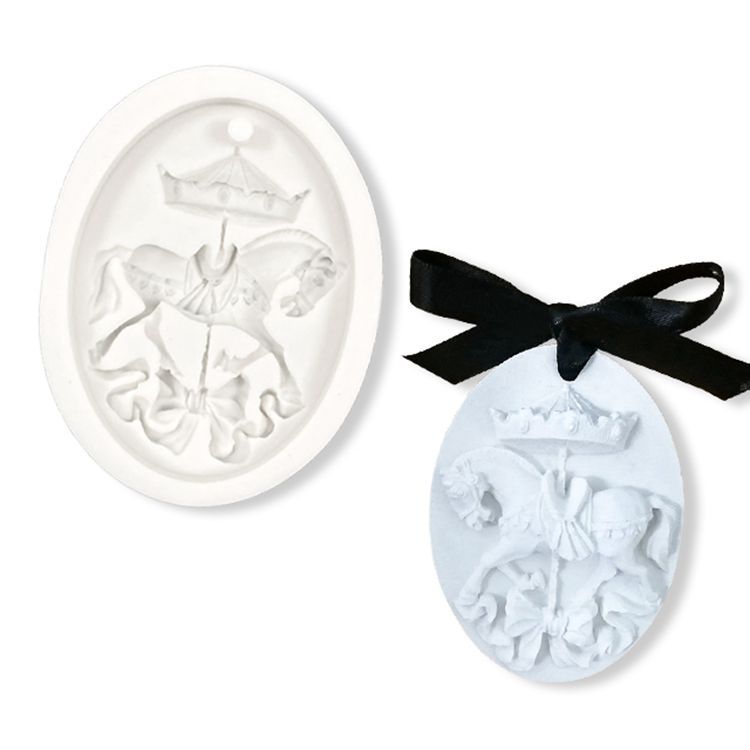
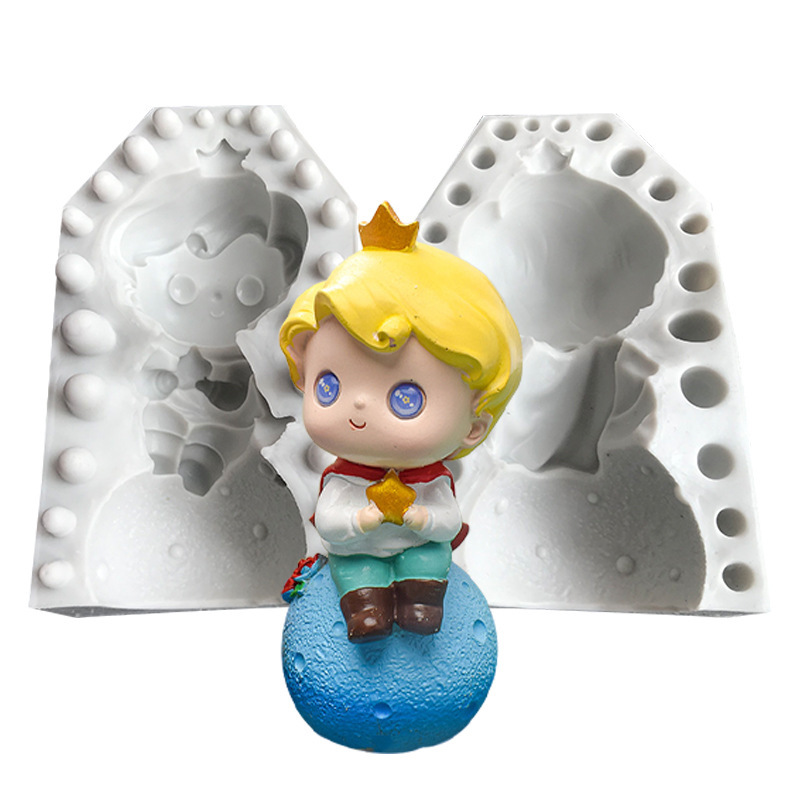
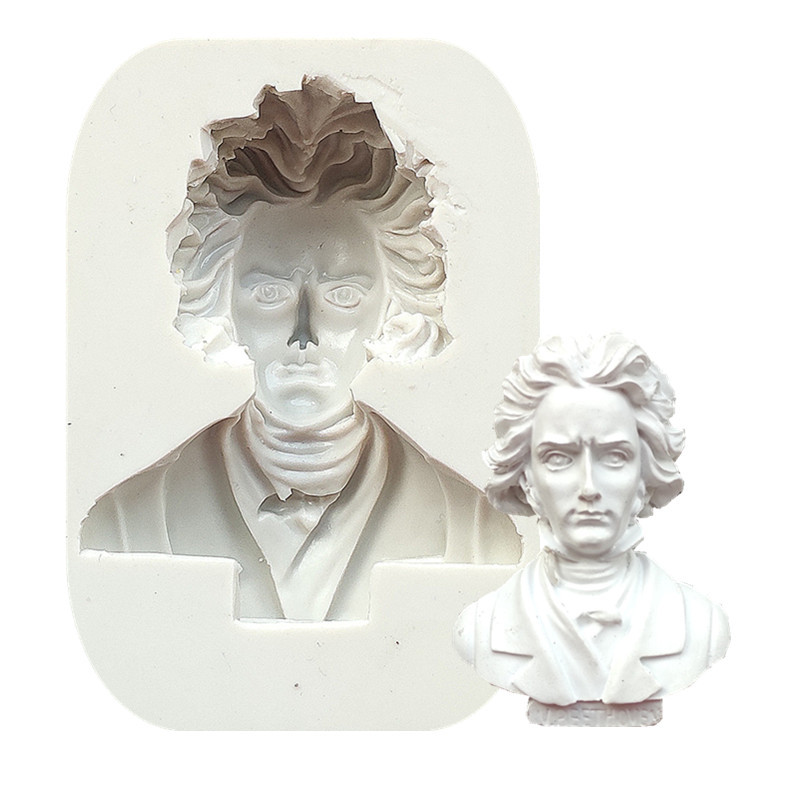
20 degrees hardness. It is suitable for making small handicrafts. It has low viscosity, good fluidity, easy operation, easy to release bubbles, good tensile and tear strength, and easy pouring.
40 degrees hardness. For large products, it has low viscosity, good fluidity, easy operation, easy to release bubbles, good tensile and tear strength, and easy filling.
If you use a multi-layer brush mold process, you may choose high-hardness silicone, such as 30A or 35A, which is easy to operate and not easy to deform.
Features
Series rubbers consist of a liquid Part B base and Part A accelerator, which after mixing at the proper ratio by weight, cure at room temperature to flexible, high tear strength, RTV (room temperature vulcanizing) silicone rubbers.They are ideal for molds where easy release or high temperature resistance is needed.They are recommended for polyurethane, polyester, epoxy resins, and wax.
Silicone rubber is used most often for casting liquid plastic resins, such as polyurethane, epoxy or polyester because the resins or the barrier coats used with them do not require release agent. Thus, plastic parts from silicone molds are usually ready for finishing with no washing of release or surface imperfections due to release agents.
Silicone molds also withstand the high temperatures (+ 250°F) of some polyester or acrylic resins or low melting metals better than any other rubber.
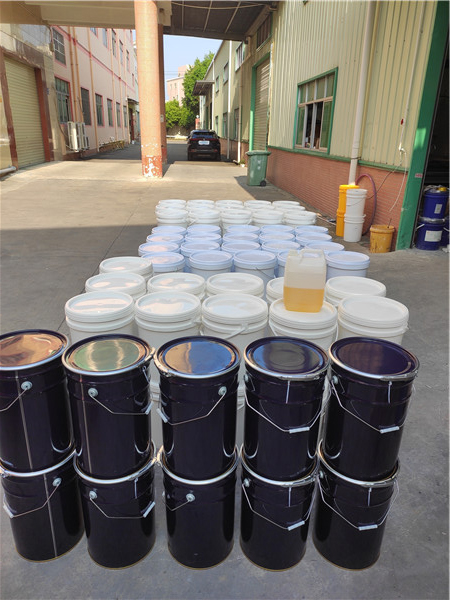
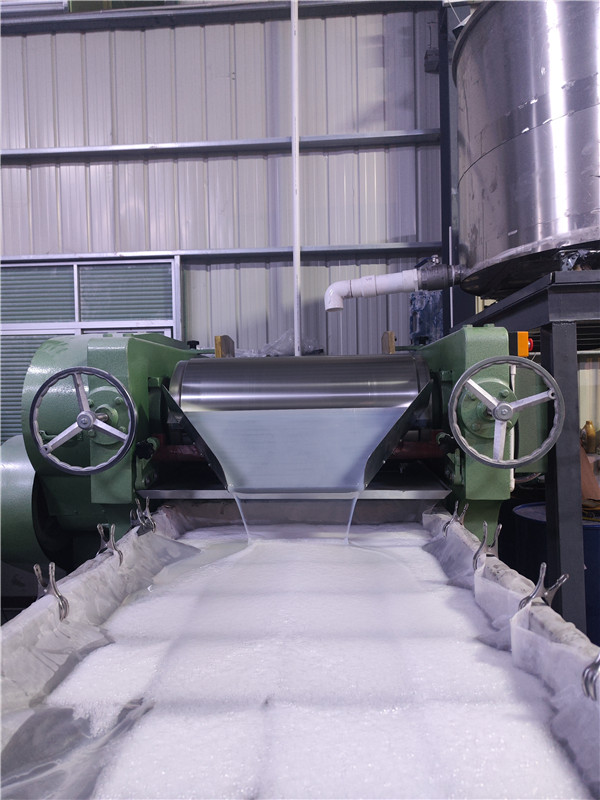
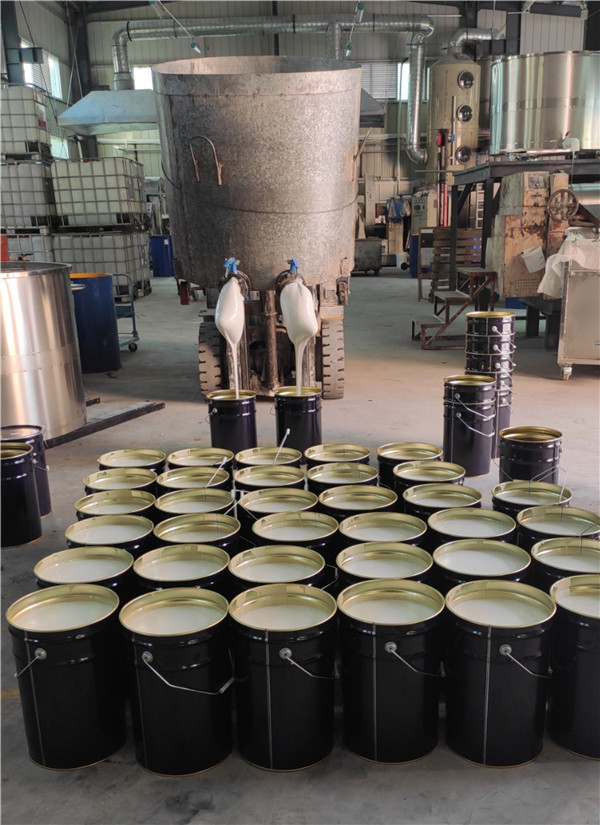