Characteristics of silicone for addition molds
1. Addition type silica gel is a two-component AB. When using it, mix the two in a weight ratio of 1:1 and stir evenly. It takes 30 minutes of operation time and 2 hours of curing time. It can be removed after 8 hours. Use the mold, or put it in the oven and heat it to 100 degrees Celsius for 10 minutes to complete the curing.
2. The hardness is divided into sub-zero super-soft silica gel and 0A-60A mold silica gel, which has the advantages of long-lasting non-discoloration and good elasticity.
3. The normal temperature viscosity of addition-type silica gel is about 10,000, which is much thinner than condensation-type silica gel, so it can be used as a raw material for injection molding.
4. Addition type silica gel is also called platinum cured silica gel. This kind of silicone raw material uses platinum as the catalyst in the polymerization reaction. It does not produce any decomposition products. It has no smell and is widely used in making food molds and adult sexual products. It is a material with the highest environmental protection level among silica gels.
5. Addition-type silica gel is a transparent liquid, and colorful colors can be mixed with environmentally friendly color paste.
6. Addition silicone can be cured at room temperature or heated to accelerate curing. Daily storage can withstand low temperatures of -60°C and high temperatures of 350°C without affecting the nature of food-grade environmentally friendly silicone.
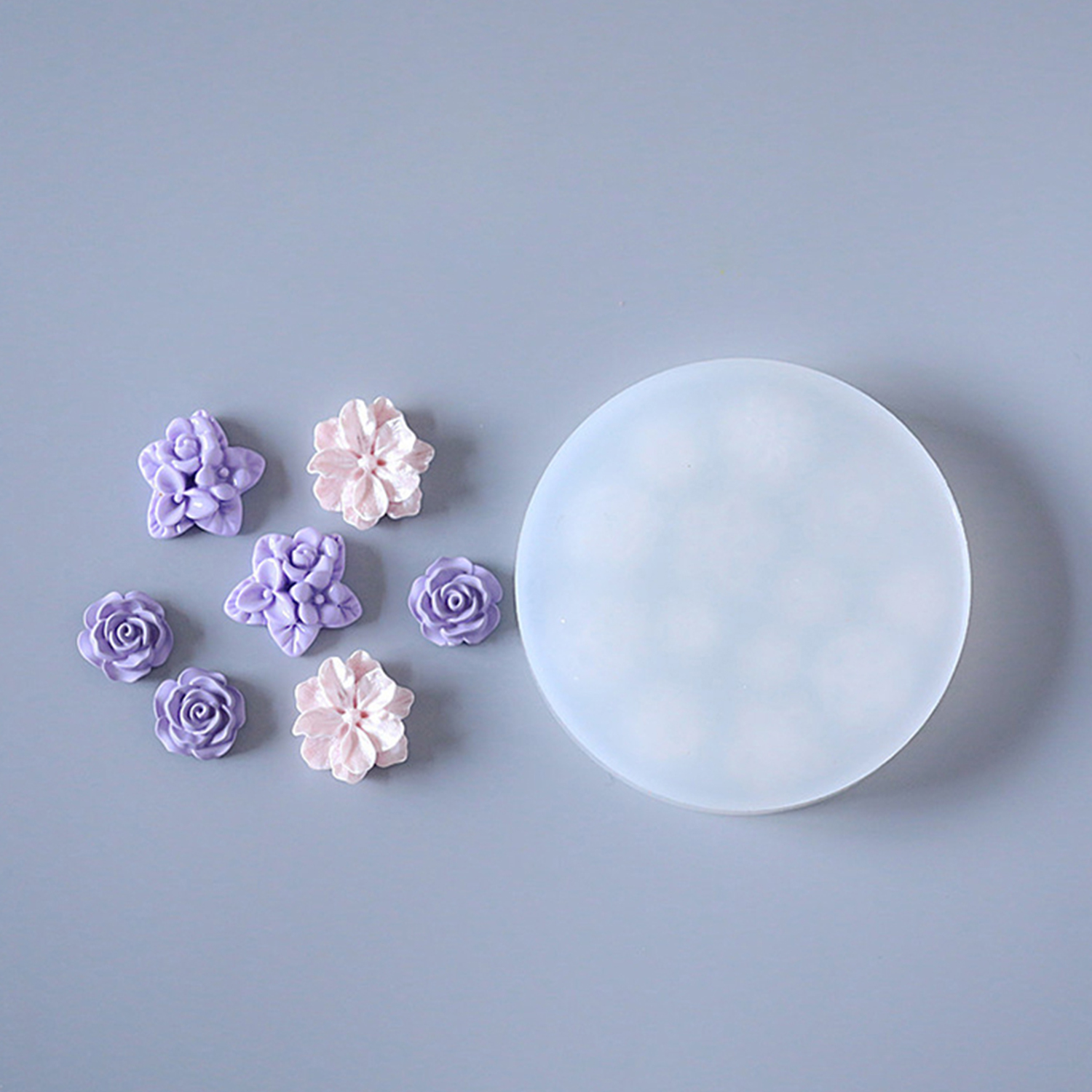
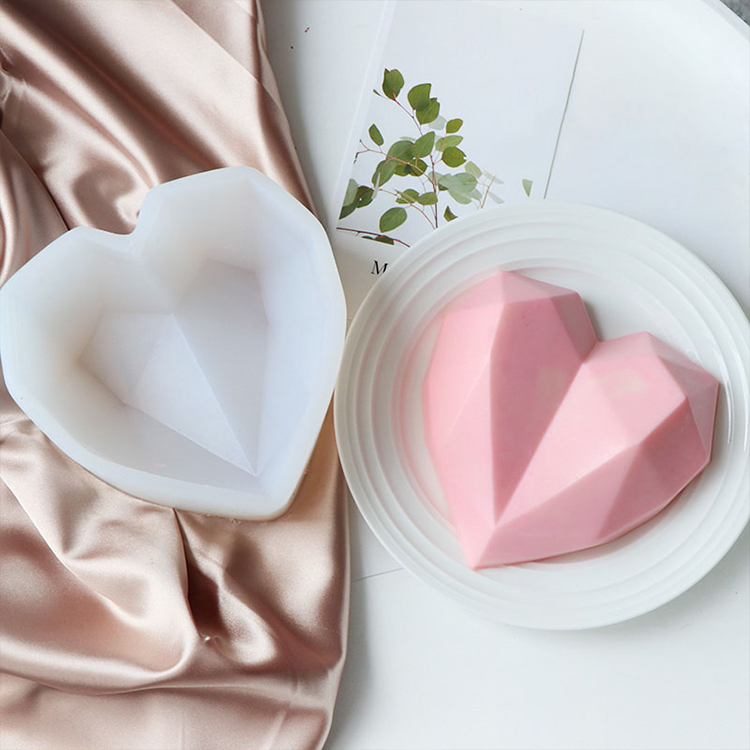
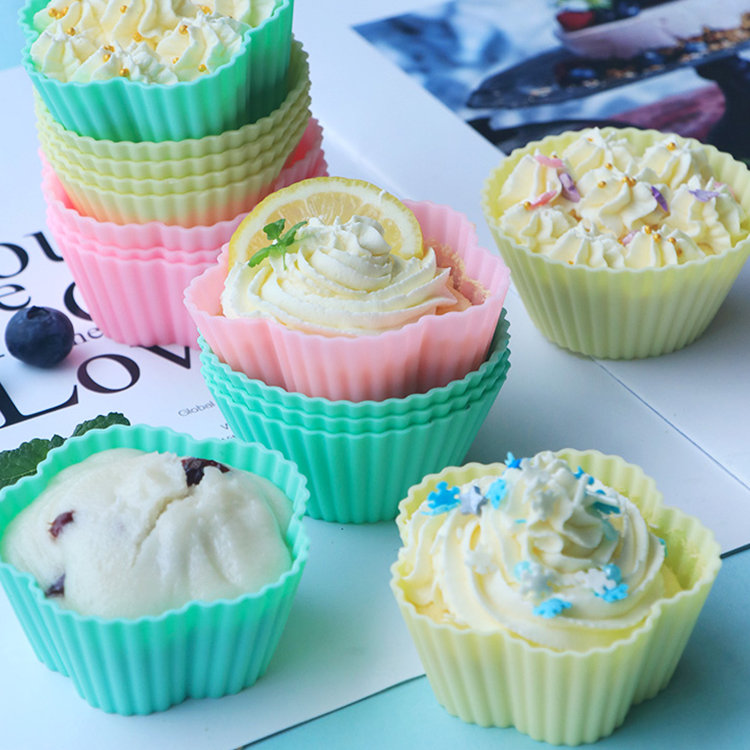
LSR 1:1 silicone mold making operation instruction
1. Cleaning models and fixing
2. Make a fixed frame for the model and fill the gap with hot melt glue gun
3. Spray molding agent for the model to prevent adhesion
4. Fully mix and stir up the A and B according to the weight ratio of 1: 1 (stir in one direction to prevent entering too much air)
5. Put the mixed silicone in the vacuum box and discharge the air
6. Pour the silicone into the fixed box
7. After 8 hours of waiting, the solidification is complete, then removes the model
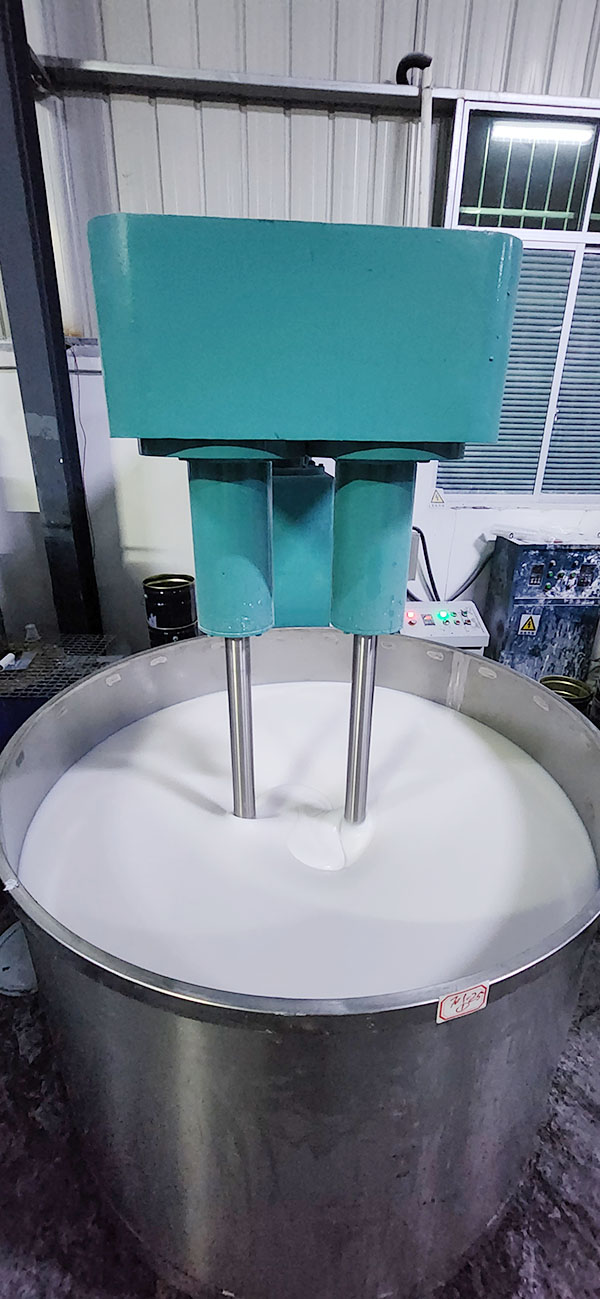
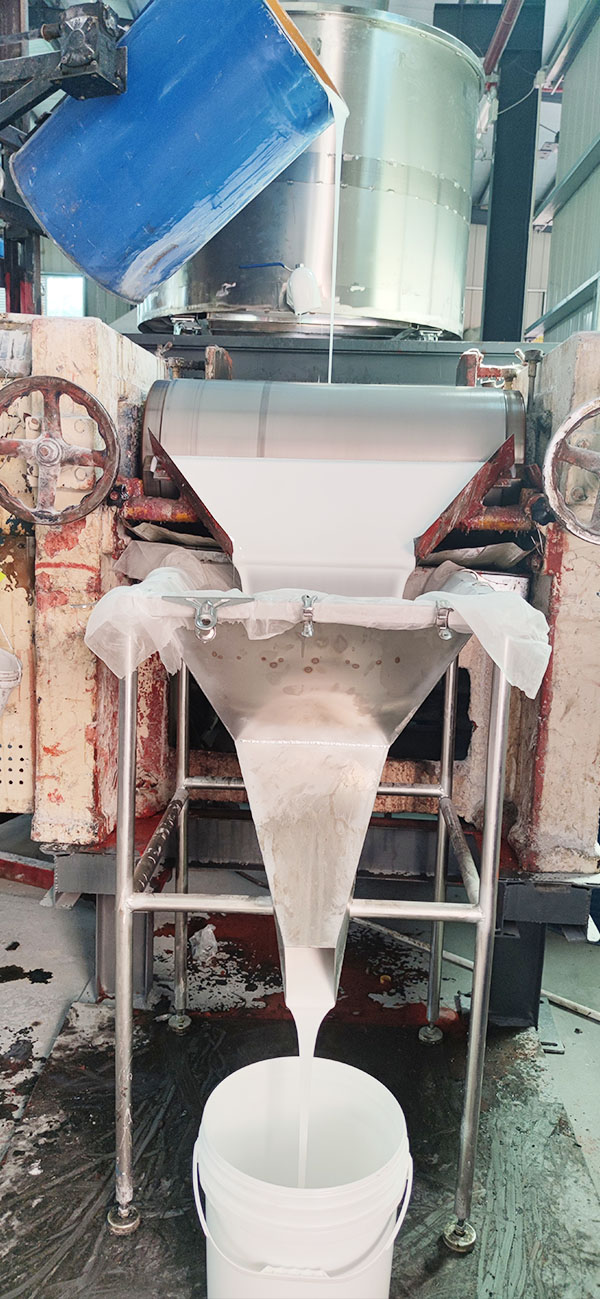
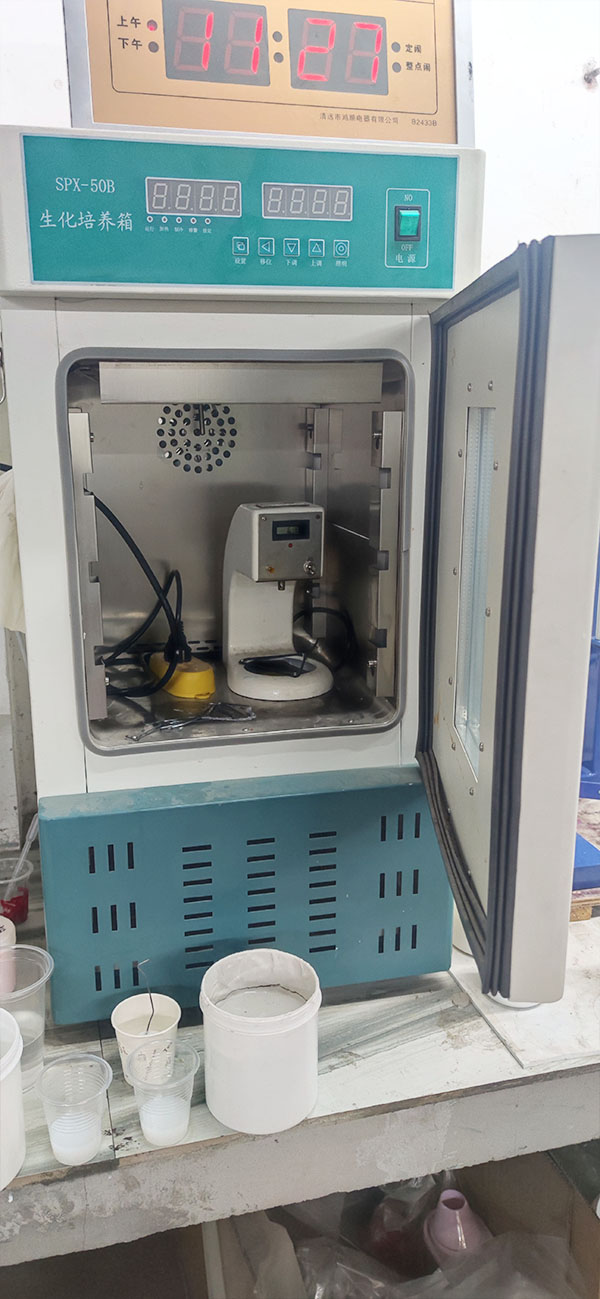
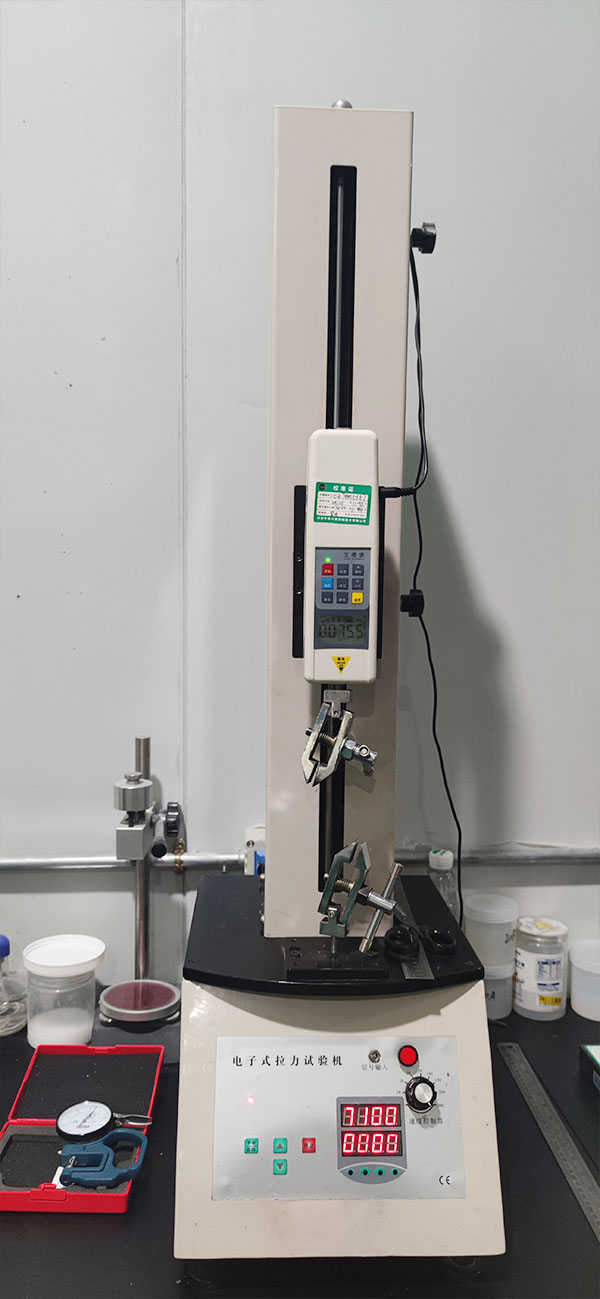
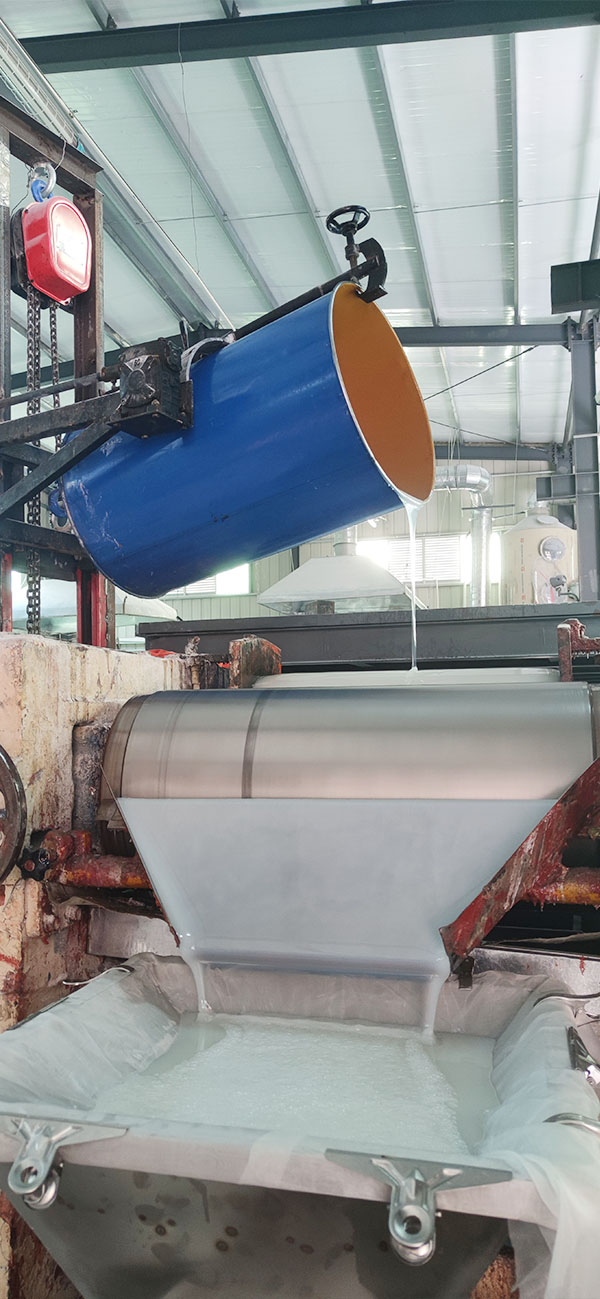