Choosing Between Silicone Molding and Injection Molding: Matching Processes to Project Needs
In the realm of manufacturing, the selection of molding processes is a critical decision, influencing the outcome, cost, and efficiency of a project. Two widely used methods, silicone molding and injection molding, each bring their own set of advantages to the table. Let's delve into the benefits of each process to better understand when and why they shine:
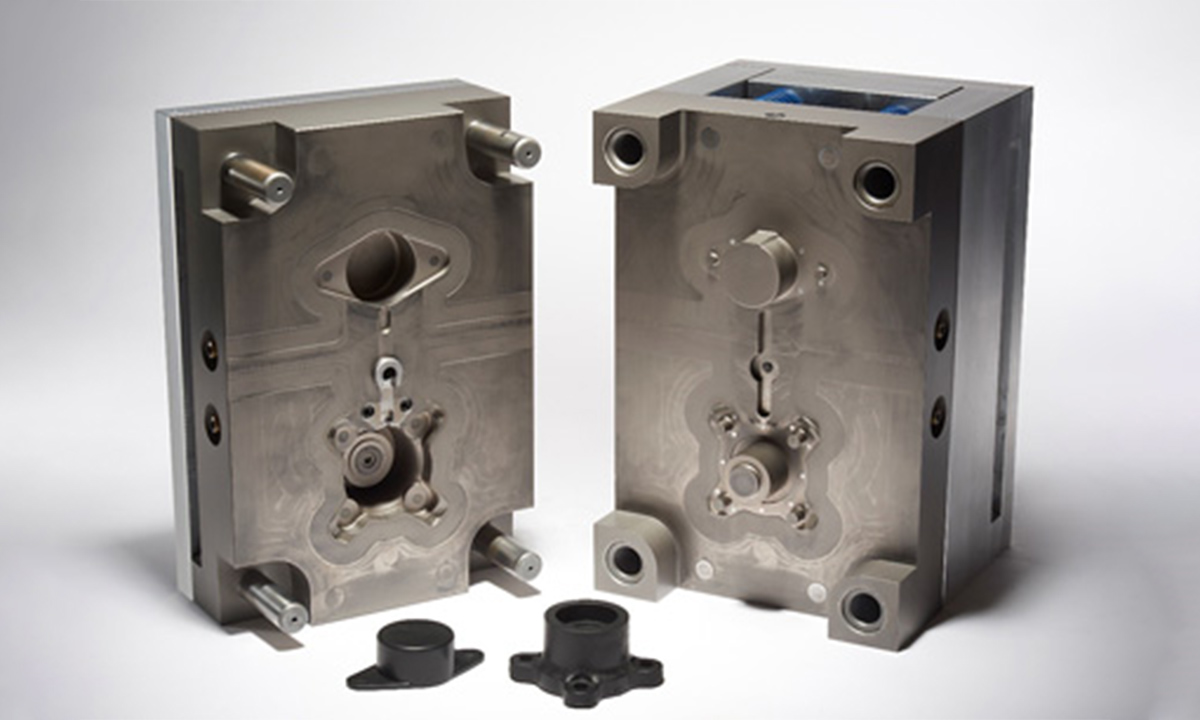
Injection Molding
Silicone Molding: Crafting Precision with Flexibility
1. Versatility: Silicone molds boast flexibility, enabling them to capture intricate details with precision. This makes them ideal for crafting complex and delicate parts, catering to industries where design intricacies are paramount.
2. Low-Cost Tooling: The tooling for silicone molds is notably less expensive than injection molding tools. This cost advantage positions silicone molding as a cost-effective solution, particularly beneficial for small production runs or prototyping phases.
3. Short Lead Times: Silicone molds can be manufactured swiftly, offering a quick turnaround for projects with time-sensitive requirements. This makes them an optimal choice for endeavors that demand speed without compromising quality.
4. Material Compatibility: Silicone molds exhibit compatibility with a diverse range of materials, from resins and foams to low-temperature metals. This flexibility in material options enhances their suitability for various manufacturing needs.
5. Low Pressure: The molding process for silicone involves lower pressure, making it particularly suitable for materials sensitive to high pressures and temperatures. This gentle approach ensures the integrity of delicate materials.
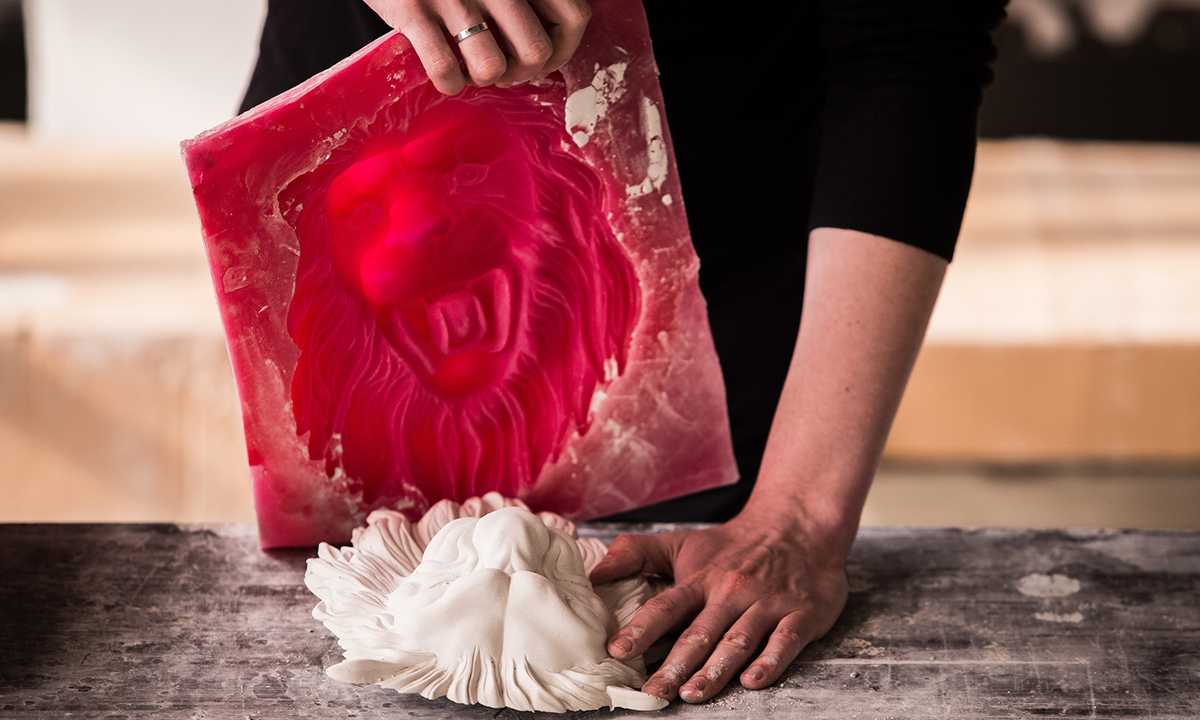
Silicone Molding
Injection Molding: The Efficiency of High-Volume Precision
1. High Volume Production: Injection molding takes the lead when it comes to high-volume production. Its efficiency and speed, once the initial tooling is in place, enable the automated production of large quantities of parts, making it a go-to choice for mass manufacturing.
2. Consistency and Precision: The injection molding process guarantees high repeatability and precision, crucial factors for industries where consistent quality across all produced parts is non-negotiable. This reliability is particularly valued in sectors like automotive and electronics.
3. Wide Material Range: Injection molding supports an extensive array of materials, spanning engineering plastics, elastomers, and metals. This versatility makes it applicable to a broad spectrum of industries and applications.
4. Complex Shapes and Tight Tolerances: The precision achievable with injection molding allows for the creation of intricate geometries and tight tolerances. This makes it the method of choice for parts requiring a high level of detail and accuracy.
5. Cost Efficiency (for Large Runs): While the initial tooling cost may be higher, the per-part cost decreases significantly with larger production quantities. This cost efficiency in large-scale operations positions injection molding as the preferred choice for those seeking economies of scale.
Choosing Wisely: Matching Process to Project
In conclusion, the decision between silicone molding and injection molding hinges on several factors, including the desired quantity of parts, design complexity, material requirements, precision specifications, and budget constraints. For smaller runs, prototypes, or intricate parts, the flexibility and cost-effectiveness of silicone molding may prevail. However, when aiming for high-volume production, consistent quality, and cost-efficiency, injection molding often emerges as the optimal solution. The key lies in understanding the unique strengths of each process and aligning them with the specific needs of the project at hand.
Post time: Jan-19-2024